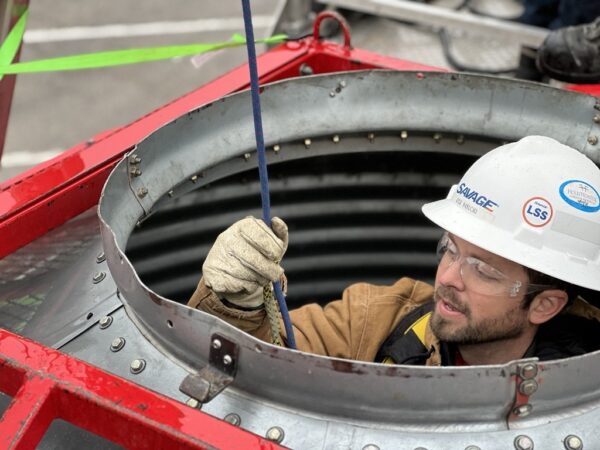
Savage Aims to Raise the Bar for Workplace Safety
For over 75 years, Savage has been elevating the design, building, operating, and maintenance processes of Customers’ supply chains. That type of experience is vital as Savage strives to develop the industry’s best practices. Efficiency, cleanliness, and singleness of vision are all highly sought-after qualities, especially as competition grows. Savage understands, however, that these are all byproducts of workplace safety.
The Big Picture
Safety is a guiding principle for how Savage Team Members operate. As such, the goal of our Safety, Health, and Environment (SH&E) team is to help each operation consistently achieve the most important milestone of efficiency: zero incidents. We accomplish this by:
- Educating Team Members to preemptively identify and correct unsafe conditions.
- Coaching Team Members on the safest choices and behaviors.
- Setting and maintaining a safety standard at every level of the company.
- Ensuring that the right lessons are learned from every incident, big or small.
Team Members who dedicate themselves to this mindset enter into what Savage’s SH&E team has termed the Personal Safety Commitment, to raise the bar of workplace safety. They become drivers of success.
Education is the Key to Workplace Safety
As a leader in the material handling, transportation, and processing space, the Savage family of companies serves many industries. Each industry requires specialized knowledge on the part of the Team Member to do their job effectively. This is especially true for workplace safety.
The SH&E team acts as Savage’s primary safety educators and drivers of the company’s safety culture. Simply put, their job is to explain how to stay safe and empower their Team Members to raise the bar. Bryan Hoggan, Vice President of SH&E at Savage, believes that one of his team’s objectives is to help Team Members appreciate the nuance of what it means to be safety-oriented. “I’m not in favor of saying that ‘safety is a priority,’” he explains. “Priorities change. Safety is a value, and when you have something you value, you always do it.”
Helping Team Members adopt the values of the company as their own is part of the challenge to raise the bar. To achieve this, the SH&E team:
- Creates a proprietary curriculum as part of Savage’s Safety Specialist program.
- Performs on-site inspections.
- Carries out an annual month of safety education initiatives.
Working in tandem, this approach to safety education can result in a measurable outcome of success — namely, fewer incidents.
“You talk to some sites, and they’ve gone years without an incident,” said Terry Bleckner, a senior SH&E manager at Savage. “And this is by deliberate design.” In his experience, this is a melding of various factors such as proactivity, selflessness, and utilizing the right safety tools. “Our tools are simple and effective, and they get good results.”
Promoting Safety Through the Safety Specialist Program
Among the most effective of these tools is the Safety Specialist program. Here, Savage Team Members are selected from across the company to attend a multi-day course to be trained as a frontline safety champion and extension of the SH&E team. These individuals are chosen for their natural leadership skills, positive attitudes, and willingness to help their fellow Team Members. In short, the very best at each operation is chosen to become a Safety Specialist.
Safety Specialists then:
- Collaborate with Team Members and site leadership on safety initiatives.
- Teach safe practices both formally and by example.
- Become one of the primary drivers of safety on-site.
Kiki Mulliner, an instructional designer and technical trainer for the program, breaks down the reasoning behind this model. “We have over two hundred sites and fewer SH&E professionals,” Mulliner said. “It doesn’t work out, math-wise, to have someone at every site twenty-four-seven … We need someone there who is looking out for safety.”
One of the greatest responsibilities Safety Specialists have is to mentor their Team Members on all the aspects of safety that pertain to their operation. Currently, there is at least one Safety Specialist – usually more – at every operation in the company.
Safety Specialists Can Become Lead Safety Specialists
Graduating the Safety Specialist course is not the end of the program, however. After a year, Safety Specialists can then choose to raise the bar and apply to become a Lead Safety Specialist. The crux of this promotion, explains Mulliner, is coaching and leadership. “The Lead Safety Specialist is responsible for a lot of the S7 items and to mentor their regular Safety Specialist counterparts.”
With Safety Specialists at every operation in the company, and SH&E Team Members consistently visiting for on-site inspections, the effect on workplace safety can be monumental.
Bleckner cites this as an extension of Savage’s Vision and Legacy. “Our mantra of continuous improvement blends into safety. A Safety Specialist will look around the operation where they work and say ‘Hey, have we thought about a better way, a safer way?’” True to the Safety Specialist mission, this enthusiasm drives Savage to raise the bar of workplace safety, and it all starts with empowering and educating the frontline Team Members.
The SH&E Team Maintains the Safety Standard
Having a safety-oriented culture means that teaching and learning never stops. Part of the SH&E mission is to help Team Members think broadly about safety and maintain the highest standards.
Hoggan notes that one of the biggest obstacles in elevating workplace safety is the moment-to-moment choice it presents workers who want to get their projects done quickly. “One of the paradoxes of safety,” says Hoggan, “is that doing things the safe way usually takes longer; it requires more steps or a bigger effort. So, our mission surrounds the question, ‘how do we make the safe path, the safe choice, the easier option?’”
To accomplish this, the SH&E team increases the points of contact between Team Members and the safety culture, such as:
- Fine tuning the onboarding process to reduce the risks of bringing on someone new to the team;.
- Increasing opportunities for Team Members to receive safety training and certifications. This may include subsidizing a secondary education to become a Certified Safety Professional, or taking part in the aforementioned Safety Specialist program.
- Collaborating regularly with Savage’s upper leadership to strategize how to develop and reinforce proper safety practices, company-wide.
“One thing I love about working with Savage is, from the CEO, all the way to the frontline forklift operator, safety’s embedded in what we do,” says Bleckner. “Safety is the first thing we talk about, and leadership is always engaged with what’s going on safety-wise within our company.”
Leadership Takes a Front-Seat Role in Safety
Involving leadership at every level is key to maintaining that company standard. The National Security Council outlines what a good safety leadership looks like. Qualities include:
- Collaboration
- Action orientation
- Feedback
- Accountability
Mulliner is quick to assert that when it comes to setting the safety standard, Savage leadership is highly involved in all these ways and more. Speaking about the Safety Specialist training, she mentions, “leadership does an hour of strategy with the Safety Specialists. And then, the other thing we do is involve leadership in Safety Specialist graduation. We even did this in Canada and Mexico.”
The result? Team Members commit to Savage’s high safety standard and report fewer incidents because of it.
We Raise the Bar for Safety When We Learn from Our Mistakes
Naturally, a supply chain company like Savage is going to have protocols in place if an incident does occur. While it may be uncomfortable to talk about, the future of workplace safety depends on learning the lessons that incidents can teach us.
“It’s unfortunate when we have an incident,” says Bleckner, “and it’s all in vain if we fail to learn and get better from it.” The SH&E department trains Team Members on how to respond to workplace incidents. Steps include:
- Ensuring every person is out of harm.
- Notifying the proper emergency and leadership personnel.
- Carrying out an internal investigation process.
Incidents tend to occur when people take shortcuts over safety protocols and/or work in unsafe conditions. When that happens, it’s important to identify the issues and then coach Team Members to prevent future occurrences.
“We have a great team of SH&E Professionals,” says Hoggan. “People that really know what they’re doing. We do a lot of work with our team to be proactive and preventative, investigating injuries and incidents that have taken place and making recommendations on how we can keep them from happening in the future.”
Be Bold and Be Better
Savage enjoys a fruitful relationship with many Partners and Customers across the globe. Through those relationships, Team Members have had opportunities to do things they never dreamed possible. The goal every day is to seize those moments in as safe a way as possible.
“There’s a quote from Emerson that I learned early in my life that I like to apply,” says Hoggan. “‘That which we persist in doing becomes easier to do, not that the nature of the thing has changed but that our power to do has increased.’ We must be bold; we must be courageous; we must be better.”
The crux of Savage’s success lies in how its Team Members raise the bar for workplace safety. Thanks to the tireless efforts of dedicated SH&E professionals and engaged Team Members on-site, Savage will continue to bring its culture of safety to many more operations in the future.