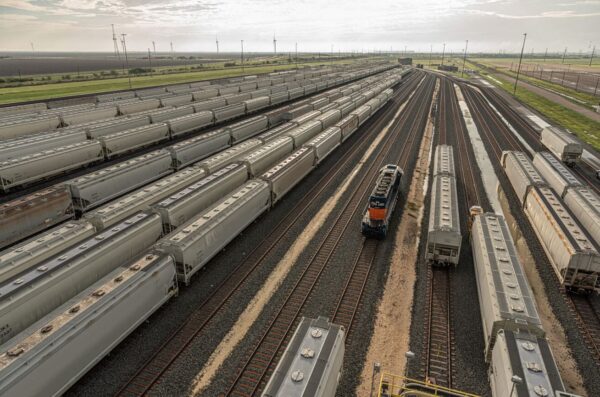
Case Study: How Savage Increased Savings and Operability for a World-Class Petrochemical Facility
Savage works with many Partners operating in the refinery, energy, petrochemical, and agricultural spaces. One of these partnerships in the plastics industry developed prior to building one of the largest processing and distribution plants in the world.
Prior to partnering with Savage, our Customer, known as an industry-leader in the petrochemical market, had relied on internal teams to design and build their facilities. This sometimes resulted in difficulties in the design and build stages that could otherwise be avoided when partnering with a more experienced construction company. Realizing this, the Customer chose to team with Savage to build their new rail operation.
The Customer’s goal was to build a polyethylene facility that could capitalize on the abundant, inexpensive natural gas feedstock in North America. This resource is used to produce plastics that are found in numerous everyday products.
The resulting facility helped the Customer achieve a greater level of operability and see certain long-standing sustainability goals realized.
Challenges
The Customer wanted to build a polyethylene cracker big enough to accommodate the scope of their worldwide business. At that time, the proposed design would make it the largest of its kind. The Customer was aware of the challenges a project of this size could bring to cost, operability, and their supply chain processes. They needed a partner with answers.
Category | Challenge |
---|---|
Cost | Troubled project management, or the wrong partner, can sink a budget with compounding costs. A more experienced company with expertise in these areas would need to help them design at a discount. |
Operability | A facility of this caliber requires deep supply chain understanding from those who have operated facilities throughout the world. Designing this facility from an operator’s perspective was critical for efficient intermodal transportation and product handling. |
Sustainability | A plastics facility is prone to numerous sustainability issues, including properly handling nurdles and cleaning spills. To avoid this, better processes must stay top-of-mind from the earliest design phase to daily operation. |
Solutions
Savage worked alongside five respected construction companies to design, build, and finance the facility. Later, Savage expanded its role to handle operations at the facility. Special attention was given to helping the Customer achieve a fully integrated design plan, one that kept efficiency and operability top of mind — in short, to design like an operator.
Category | Solution |
---|---|
Cost | With Savage overseeing engineering and construction, the rail facilities were delivered on time and on budget in the face of the COVID-19 pandemic. |
Operability | Savage’s input led the Customer and the partnering Class 1 railway to make needed changes to the infrastructure that enhanced the project’s operability. This included iterating on the Customer’s railcar loading system to improve its efficiency. |
Sustainability | By designing like an operator and iterating on the best practices from groups like The Nurdle Patrol, the facility runs smoothly, safely, and cleanly, setting a new standard in plastics sustainability. |
“…this has been the most enjoyable contractor relationship I’ve ever dealt with, and the most impressive in my 15-plus years overseeing projects across the world”
–Project Manager with the Customer
Results
Thanks to compounding successes in both sustainability and supply chain operation, the Customer has become a gold standard in how to design, build, finance, and operate new infrastructure, especially in the plastics industry. By leveraging their own experience – and the experience of partners like Savage—they recognized processes that could be improved and developed a long-standing partnership to correct them. Savage is proud to have assisted in a project that was delivered on time and under budget.
Download the Petrochemical Facility Case Study